In this paper, through the research and analysis of the structural fracture problem of the failed parts, under the constraints of the actual design space and cost, we can find a reasonable optimization structure and find an easy-to-implement and economical solution in the project.
This article refers to the address: http://
First, the question is raised
In the development of new products, the reliability of the structure requires a batch life test. In the batch life test of the parts shown in Fig. 1, in the one percent probability sample, the crack occurred in the convex columnar structure a, resulting in failure of the full set of mechanism functions. Figure 2 shows the fracture state of the part failure structure.
  
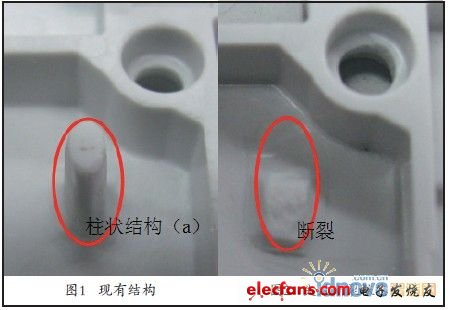
Â
  
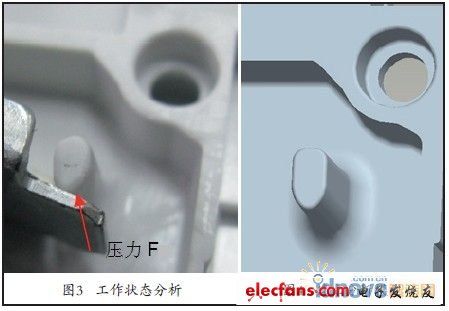
Â
The working state of the structure is analyzed. As shown in Fig. 3, the surface of the columnar structure is subjected to the periodic pressure F of the metal part, and the magnitude of the pressure F can be obtained by a dynamometer. In the actual operation, the columnar structure a is also affected by the small impact force and the ambient temperature and humidity in the working state. In the analysis of the problem, combined with engineering experience, the pressure F is the main influencing factor of the fracture. For this reason, the condition can be simplified, and the abstract analysis model can be obtained according to the main reason (see Figure 4), and then the Nastran analysis.
Second, based on finite element Nastran analysis and optimization
1. Structural stress concentration analysis
Using the analysis process of finite element analysis software Nastran, the model is simplified first, the stress deformation analysis of the existing structure is carried out, the structural stress concentration position causing the fracture is found, and then the next structural optimization is carried out.
The material properties are defined, and the irregular model is meshed by the 3D mesh 10 node unit. In order to ensure the accuracy and precision of the calculation, local mesh refinement is performed. Set reasonable boundary conditions, apply effective uniform load F after analysis of actual state; select structural static linear solver to solve, and grasp the main factors to quickly find the problem. There are many factors that cause fracture in actual situations. If a nonlinear solver is used, the computational complexity will be caused, and it is difficult to find a solution quickly. Figure 5 shows the results of the meshing and the location of the applied load. Figure 6 shows the results of the stress concentration analysis. It can be seen from the analysis results that there is stress concentration at the position of the 1st column in the columnar structure, and it is necessary to strengthen the structure for the force condition, and at the same time ensure that the movement of other parts around the columnar structure is not affected.
  
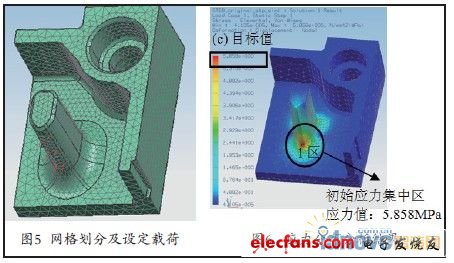
Â
First determine the areas that can be optimized under engineering conditions. The optimization of the structure must ensure that the normal movement of the mechanical parts is not interfered with, and the structural improvement is carried out within the practical allowable range. In this paper, the area required for the motion mechanism (see Figure 7) in the working state is measured to find the area where the structure can be optimized, and the structure can only be optimized within this limited range. The horizontal direction of the optimized region of Fig. 7 is indicated in the model, and Fig. 8 is a limited range in the height h direction that does not interfere with the motion of the mechanism.
  
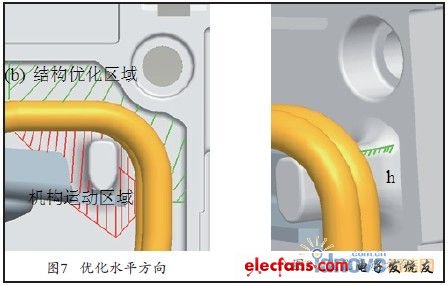
Â
Second, determine the achievable optimization goals. Under the requirement of ensuring the strength of the column structure without breaking, the changed structure is minimized, which not only reduces the workload and cost of mold modification, but also saves raw materials.
According to the basic theory of mechanics, under the same conditions of the force application surface, the applied load is proportional to the stress. Through experimental tests, the average pressure that the columnar structure can withstand in the failed sample is 9N. Above this pressure, the structural stress increases and the probability of fracture increases.
Under actual working conditions, the columnar structure has to withstand an average pressure of 12 to 13 N, so that it will break beyond the stress limit it can withstand. This requires the improvement of the structure to reduce the stress and increase the strength of the structure. When the load is applied, the stress is within the limit, and the structural strength requirement can be achieved. Calculate the stress distribution under the condition of 9N. As shown in Fig. 6, the calculation result is 5.858 MPa, which is the optimized ultimate stress target value, that is, the optimized structural stress needs to be close to the target value.
Once again, the idea of ​​structural optimization is determined, and the structure is improved based on theory and engineering experience.
According to the theory of material mechanics,
  

Â
Increase the bending section modulus without changing the load application state
  

Â
Can reduce stress. Analyze the cross section of the columnar structure so that the position of the neutral axis is close to the point of application, which can increase the modulus of the bending section; increase the thickness of the bottom and reduce the stress concentration. The optimization of the specific structure size can be calculated by software, and a more optimized scheme can be obtained after comparing various analysis results.
Under the condition of 13N load, the structure is optimized and the stress distribution result is calculated. As shown in Fig. 9, when the load is increased from 9N to 13N, the stress value in the original stress concentration region is reduced to 3.718 MPa.
As shown in Fig. 10, the optimization of the structure eliminates the existence of local large stress concentration. In the case of a load increase of 30% in the maximum stress zone, the stress value is slightly smaller than the optimization target value, which is 5.835 MPa. It shows that the structural strength is greatly enhanced, and the optimized structure can withstand the load under the existing working conditions.
  
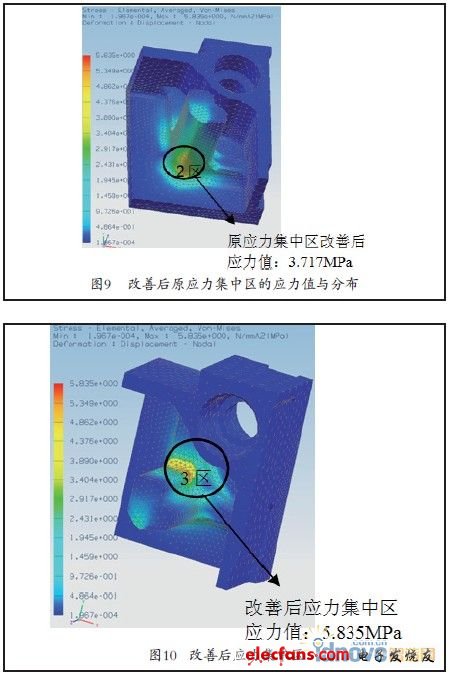
Comparing the optimization results, the maximum stress value before and after optimization and the change of the stress value in the original stress concentration region are given by Fig. 11, corresponding to the 2 and 3 regions in Fig. 9 and Fig. 10, before the load is optimized. When 9N is increased to the optimized 13N and the load is increased by 30%, the maximum stress value is slightly reduced, and the local stress concentration phenomenon is significantly improved (see the 2-zone curve in Fig. 11). By optimizing the structure, the stress in the initial structural stress concentration region is reduced by 36.5% (see the 3-zone curve in Fig. 11). The optimized load capacity of the structure is enhanced and the reliability of the parts is improved. The final optimized shape determined by the model is shown in Figure 12.
  
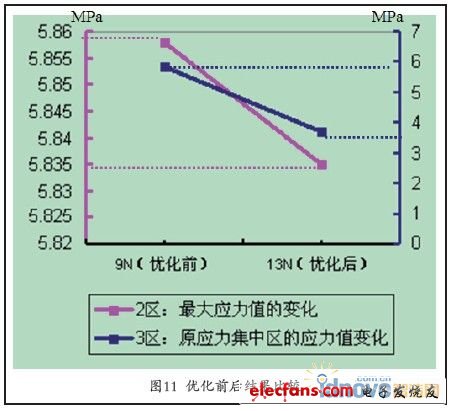
Â
  
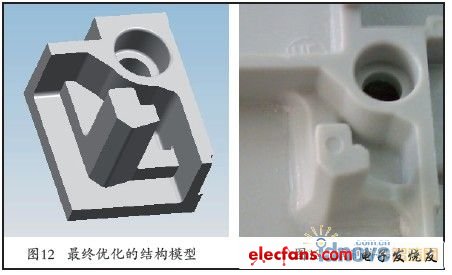
Â
Third, based on the optimization program of the sample test and comparison
According to the result of the optimization of the scheme, the mold is improved, and the sample parts are prototyped, as shown in FIG. The batch life test was carried out, and the optimized convex columnar structure was free from fracture, and was 100% qualified. Structural reliability is effectively enhanced by optimizing the structure.
Fourth, the conclusion
In this paper, based on the problem of structural failure of parts in engineering, a method and method based on finite element analysis software Nastran is proposed to solve the problem. Based on the theory of mechanics and engineering experience, NX-Nastran is used to analyze and optimize the failure structure of the part; find a better solution to guide the improvement of the mold in the actual manufacturing, make the sample to test and solve the part structure. The failure problem improves the reliability of the part structure, reduces the cost of mold modification, shortens the time, and verifies the correctness of the software analysis. It reduces the research and development cost to a certain extent, accelerates the process of product development, and has certain reference value for solving similar problems in engineering applications.
Led Linear High Bay Light from Bbier is the LED replacement for fluorescent tube lighting fixtures,Led Linear High Bay is the ideal replacement for traditional fluorescent lighting in warehouses and other large interior spaces.ideal for aisles or high ceilings,Use for warehouses,gymnasiums,garages,conference rooms,retail space,and other large indoor facilities.Linear High Bay Light series are DLC Listed & ideal for one-to-one replacement for conventional HID, T8 and T5.LED linear high bay fixtures available in different ... sizes, and color temperatures to suit your high bay lighting needs. these Linear Led High Bay fixtures are a great value with dependable performance.The Summit LED linear High Bay is an ideal one-to-one replacement for conventional HID and fluorescent lighting systems in large indoor spaces.This LED Linear High Bay is a brand new replacement solution for fluorescent linear high bay in warehouses.
Led Linear High Bay,Led Linear High Bay Light,Linear High Bay Light,Linear Led High Bay
Shenzhen Bbier Lighting Co., Ltd , https://www.chinabbier.com